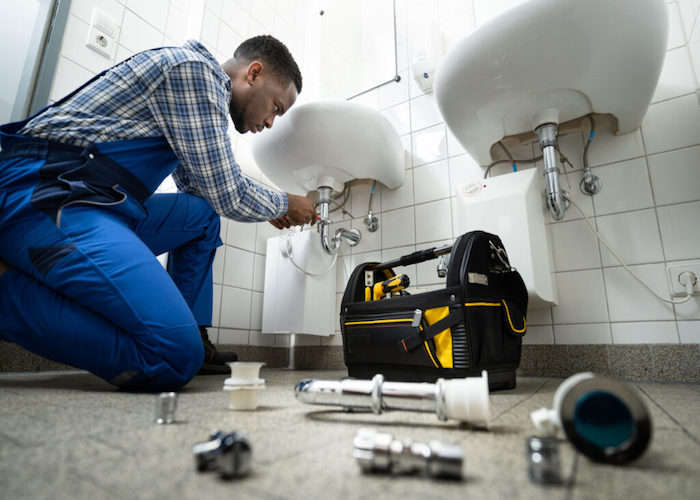
Technical specifications for plumbing nashville work outline the standards, materials, and methods required for the installation, maintenance, and inspection of plumbing systems. Here’s a detailed guide covering the key technical specifications:
1. General Requirements
1.1 Compliance:
- All plumbing work must comply with local building codes, national standards (e.g., International Plumbing Code (IPC), Uniform Plumbing Code (UPC)), and industry best practices.
1.2 Permits and Inspections:
- Obtain necessary permits before commencing work.
- Schedule inspections at various stages of the project as required by local authorities.
2. Materials
2.1 Pipes:
- Copper: Type K (thickest walls, underground), Type L (medium walls, residential and commercial), Type M (thinner walls, low-pressure applications).
- PEX: Cross-linked polyethylene, suitable for hot and cold water supply, color-coded (red for hot, blue for cold).
- PVC: Polyvinyl chloride, Schedule 40 for general use, Schedule 80 for higher pressure applications, used for cold water and drainage.
- CPVC: Chlorinated polyvinyl chloride, suitable for hot and cold water supply, more heat-resistant than PVC.
- Galvanized Steel: Used for water supply in older homes, prone to corrosion, not commonly used in new installations.
- Cast Iron: Used for drainage, waste, and vent (DWV) systems, durable, noise-reducing.
2.2 Fittings:
- Elbows, Tees, Couplings, Unions: Made from materials compatible with the pipes they connect (e.g., copper, PVC, PEX).
- Adapters, Bushings, Caps, Plugs: To transition between different pipe sizes or types and close pipe ends.
- Valves: Ball valves, gate valves, globe valves, and check valves for controlling water flow.
2.3 Fixtures:
- Sinks, Faucets, Toilets, Showers, Bathtubs: Must meet performance and efficiency standards, such as WaterSense for water conservation.
- Water Heaters: Electric, gas, or tankless, sized according to demand and meeting energy efficiency standards.
3. Installation Procedures
3.1 Water Supply System:
- Main Supply Lines: Install with a slope for proper drainage, use appropriate fittings and supports, test for leaks under pressure.
- Branch Lines: Run from main supply lines to fixtures, avoid sharp bends, use expansion loops or offsets to accommodate thermal expansion.
3.2 Drainage, Waste, and Vent (DWV) System:
- Drainpipes: Slope at least 1/4 inch per foot towards the sewer or septic system, use long sweep elbows for direction changes.
- Vent Pipes: Extend through the roof or to an outside wall to allow gases to escape, maintain proper distance from windows and air intakes.
- Traps and Cleanouts: Install P-traps under sinks, tubs, and showers, provide cleanouts at strategic locations for maintenance access.
3.3 Fixture Installation:
- Sinks and Faucets: Secure to countertops or walls, connect supply lines with flexible hoses, test for leaks.
- Toilets: Secure to the floor with bolts, connect to the flange, ensure proper sealing with a wax ring, test flush mechanism.
- Showers and Tubs: Install on a level surface, connect to hot and cold supply lines, ensure proper drainage and sealing.
3.4 Specialized Installations:
- Water Heaters: Install according to manufacturer’s instructions, provide adequate ventilation for gas heaters, insulate hot water pipes.
- Gas Lines: Use approved materials and methods, perform leak tests, ensure proper ventilation.
- Water Filtration Systems: Install in accessible locations, connect to the main water supply, follow manufacturer’s maintenance recommendations.
4. Safety and Quality Control
4.1 Safety Measures:
- Use personal protective equipment (PPE), follow OSHA guidelines, ensure proper ventilation in confined spaces.
- Handle hazardous materials with care, dispose of waste according to regulations.
4.2 Quality Control:
- Inspect all joints, connections, and fittings for leaks.
- Ensure all installations are level, plumb, and securely fastened.
- Test systems under pressure and flow conditions to verify performance.
5. Maintenance and Testing
5.1 Routine Maintenance:
- Regularly inspect pipes, fittings, and fixtures for signs of wear or leaks.
- Clean drains and traps to prevent clogs, flush water heaters to remove sediment buildup.
5.2 Testing:
- Pressure test water supply systems before covering or concealing pipes.
- Smoke test DWV systems to identify leaks or improper connections.
- Perform backflow prevention tests annually to ensure safety.
6. Documentation and Record-Keeping
6.1 As-Built Drawings:
- Provide detailed drawings showing the actual installation layout, including pipe sizes, locations, and fixtures.
6.2 Maintenance Logs:
- Keep records of all maintenance activities, inspections, and repairs.
6.3 Compliance Certificates:
- Maintain copies of permits, inspection reports, and compliance certificates.
Conclusion
These technical specifications provide a comprehensive guide for plumbing work in buildings, ensuring that installations are safe, efficient, and compliant with regulations. Adhering to these standards helps prevent common plumbing issues, enhances system longevity, and ensures a high level of performance and safety.